Top Sources of Water Pollution on Construction Sites and How to Treat it
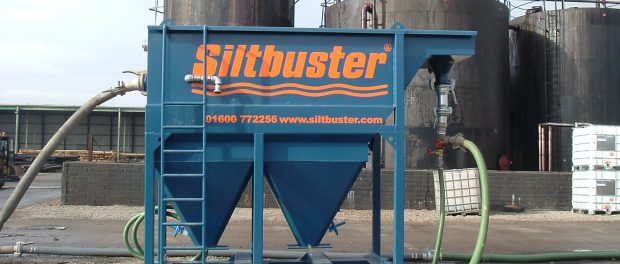
Richard. D. Coulton, General Manager – Construction at Siltbuster, the onsite site water treatment experts, outlines the typical causes of water pollution and solutions to treat them.
Without careful planning, significant water pollution incidents can far too easily arise on construction sites, especially with the wet weather we often face. The simple act of stripping a site of topsoil may create pollution when it rains. Other day-to-day building activities which involve chemicals such as, paint, solvents, fuel and cement present further risks. While if construction is taking place on a brownfield site, potential pollutants from disused storage tanks, contaminated ground and groundwater through to disused mines can all come into play.
There have been numerous examples over the last three years of companies and organisations who have taken a less than tough approach to water management, falling fowl of the increased sentencing guidelines, in some cases resulting in fines in excess of one million pounds.
The Environment Agency’s regulatory position statement “‘Temporary Dewatering of Excavations to Surface Water” (RPS) reaffirms that all contractors must have a Bespoke Permit to discharge anything other than clean water off site into the surrounding environment, therefore a suitable plan for managing common pollutants is key to ensuring compliance.
Suspended Solids (Silty Water)
The most common source of pollution on construction sites is suspended solids (silt-laden waters). This is primarily due to the ease in which it can occur.
When a construction site strips the topsoil, it takes away the land’s strongest defence against erosion, vegetation. The remaining surface has no shield or binding element to protect it from rainfall and run-off. With no plant matter to slow it down, and with the surface compacted by the use of heavy machinery, the rate of run-off increases, and the scouring effect is exacerbated. If machinery continues to operate in wet conditions, it churns up the ground, releasing soil particles that become suspended in the surface water.
While soil is a natural substance, if a significant amount of this “muddy” water enters nearby drains and watercourses, it can block the gills of fish and smother aquatic plants and invertebrates, starving them of light and oxygen.
There are practical steps construction firms can take to minimise such silt pollution. For example, only stripping the minimum area necessary, installing silt fence in areas to minimise scouring and digging cut off ditches to divert run-off from flowing though the site. However, if silty water does arise it will need dealing with – and with tankering costs being prohibitively expensive, that means mastering on site treatment techniques.
Where possible the construction of settlement lagoons will help manage suspended solids, but these take up a lot of space on construction sites. However these efforts are often hampered in areas of geology with chalk and clay due the very fine particle size and hence poor settlement characteristics.
A more compact solution is to use lamella clarifiers which are up to 20 times more space efficient than traditional baffle tanks or lagoons.
However even then, if the silty waters have fine slow settling particles, such as clays, chemical dosing stage may also be required to aggregate the particles and so increase the settling rate. Such systems can be both hired or purchased to work in conjunction with existing lagoons or with portable clarifiers.
Hydrocarbons (Oils)
Hydrocarbons are commonly encountered on remediation projects in the form of petroleum-based substances such as petrol, diesel, kerosene and oils. Sources typically range from historical spillages that have been absorbed into the land or from unmapped pipe networks still full of product or even new spillages from refuelling of plant or bust hoses.
There are some practical measures construction firms can take to minimise this pollution, such as providing oil spill kits and refuelling vehicles in designated areas where adequate spill prevention can be provided.
However, in certain cases, such as site remediation, oil contaminated water may be hard to avoid. In such cases an oil water separator will be needed which will remove the contamination. A floating hydrocarbon (light non-aqueous phase liquids) leaves the visually obvious rainbow sheen to the water, whilst a denser contaminate such as creosote will simply sink to the bottom of a tank. These can be easily separated from the water through either flotation for LNAPL’s or settlement for DNAPL’s.
However, if hydrocarbons are found to be in a dissolved phase, treatment is significantly more expensive, and typically achieved by absorbing the hydrocarbons onto carbon though the use of GAC Vessels.
Care should be taken when working with free phase hydrocarbons as selection of the wrong sort of pump can emulsify the oils, making treatment harder and lot more expensive. A low sheer pump, such as a progressive cavity or diaphragm pump are best suited to these applications.
High pH Water
The most common source of high pH water on construction sites is from the washing of concreting plant and tools, however lime stabilisation works and the re-use of crushed concrete as a recycled aggregate can also lead to an elevated pH.
On a volume by volume basis alkaline water has the potential to cause much greater harm than silt or oil. This is because the pH of concrete wash water is incredibly high – typically 12 to 13, which is equivalent to oven cleaner – making it highly damaging when discharged to the aquatic environment. Despite these risks it is much misunderstood by construction workers, for instance many allow concrete wagons to wash out in leaky waste skips.
Dilution isn’t practical or cost effective; it takes 10,000 litres of water to get 1 litres of concrete wash water with a pH of 12 to an acceptable pH of 8.
Some suggest using mineral acids like sulphuric or hydrochloric to adjust the pH. However, these are dangerous to handle, can easily overshoot the target resulting in equally polluting acidic water and they also create “secondary pollutants”. Citric acid is also easy to overdose, and it increases the water’s Biochemical Oxygen Demand above limits which are acceptable to the Environment Agency.
Given these drawbacks, carbon dioxide is by far the best neutralising agent for concrete water. It’s virtually impossible to acidify water using it, CO2 has no hazardous by-products, is easy to store and is a more cost-effective treatment.
Summary
There are some simple steps construction firms can take to both minimise the risk of creating onsite water problems and to deal with the problems should they arise. The key lesson is to be pre-emptive rather than reactive; to anticipate the problems, prepare for the unexpected and know what the solutions are – in essence, to plan.
Whenever a treatment regime is selected, it is equally critical to ensure that the a robust control system is in place to ensure accurate dosage of reagents where applicable and enable a tracible audit of the treatment regime though the use of data loggers where appropriate to provide evidence to compliance in case of inspections or to defend accusations of contamination.
For further information about treating construction site waters visit www.siltbuster.com, or visit Siltbuster on Stand G24 at Contamination Expo, which takes place on 11&12 September at Birmingham’s NEC.
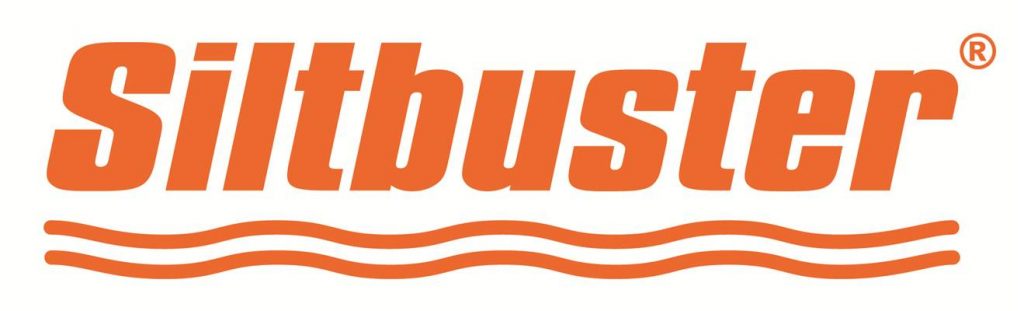