ISG makes headlines with BBC Cardiff HQ
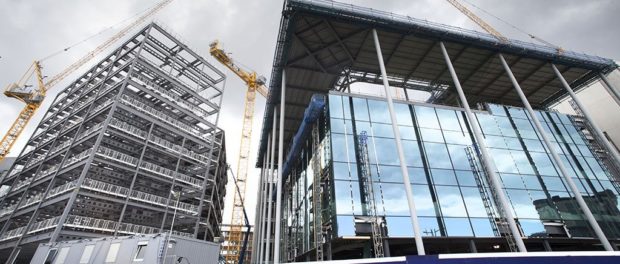
“With this project, everything is about the detail,” says ISG project director Kevin McElroy, pointing up at a colossal 2,000-tonne steel frame, which will ultimately be the floor of a rooftop garden above the BBC’s new headquarters in Cardiff.
The frame has precise connections, with some forming triangular shapes. A diamond design spans across the floor at the centre and will be left exposed underneath a glass floor.
We’re standing in the middle of what will be the BBC’s media hub, where news will be broadcast to millions across the country. “You’ll probably see Huw Edwards on the telly here,” Mr McElroy says, pointing to the edge of the floor that overlooks Cardiff Central station.
The first thing you will see stepping out of the capital’s train station will be the glittering façade of the broadcaster’s headquarters. It is part of the wider regeneration of Central Square – developer Rightacres Property Company’s flagship scheme.
The site used to be a bus station and is being replaced with office space, student accommodation, retail space, apartments and a new bus terminal.
ISG is currently building the broadcaster’s media hub, which is part of phase two of the overall scheme.
Set over four floors, the building will be the new home for 1,200 BBC Wales staff and will include 150,000 sq ft of office, studio and production space.
The contractor is now into week 73 of the 122-week project and has had to tackle a mammoth logistical challenge, making sure work on site has not stopped the city from being business as usual.
The 180,000 sq ft site, located in the heart of the city, is incredibly tight. It sits a mere 7 m from pedestrian walkways and is located on the edge of the busy Wood Street.
Mr McElroy explains that the location meant it required some rigorous planning, especially when the team was working on the substructure stage.
Around 47,500 cu m of material was removed to make way for a 75,000 sq ft basement structure, described by Mr McElroy as “something to behold”.
He explains how a mammoth mud shift was required to create the substructure, taking 40 weeks to complete after piling was installed. “A big challenge we faced was excavating the enormous volume of materials without any disruption to the operations of the city,” he says.
On average, 100 lorries were coming to and from site to remove the materials every 10-hour day. However, it was essential this mass movement did not block up the roads in and around the city centre.
The team used a self-developed traffic management app to prevent queues forming due to lorries departing and arriving.
A massive 5,588 vehicle movements were completed over a 10-week period – with no complaints made about congestion.
“The biggest technical challenge for the project was putting in the steel frame,” Mr McElroy says.
The vast frame is an essential design feature, as part of the design’s focus on the building’s visibility. The steel frame will be left exposed underneath a glass roof garden canopy, with the frame’s connections forming a diamond shape in the centre.
“The frame was a big [consideration] in the design,” Mr McElroy says. “All of [it] was manufactured off site and will be left on show. It was important for us to get the quality right.
Because of the prominent role it plays in the design of the building, it was vital the frame was left in pristine condition.
“There was a worry the steel would be cut into when we were installing it, leaving marks,” Mr McElroy explains. “We needed to make sure there was a flawless topcoat.”
In addition, 10 28.2 m-high supporting steel columns needed to be installed to prop up the roof canopy, which also needed to be immaculate.
Around five connections were made to link the columns with the main supports for the floors – which took up a lot of time, according to Mr McElroy. “We had to make sure the quality of the welds was exactly right, as when you walk through you’ll be able to see those connections. It needs to be perfect.”
All 10 columns were brought on site in a single piece, as a splice would ruin the appearance. They are the longest steel sections to leave steel contractor Severfield’s factory in Northern Ireland, according to ISG.
The contractor aims to leave behind a legacy in the Welsh capital and has been engaging with local schools, colleges and communities that will inspire the next generation to consider entering the industry.
“With a project of this size and nature, you want to promote the construction industry,” Mr McElroy says.
ISG opened its doors for local pupils to take a look at works on site and has been offering students from Cardiff and Vale College with placements on site. Mr McElroy says this provides the next generation an opportunity to gain insight into what the industry can offer.
“We also have a new trainee on site every week,” Mr McElroy says. “They can get some real experience and get motivated about the careers available to them. It’s a great opportunity for them to say, ‘I worked on that project’.”
As a scheme that is fundamental to the regeneration of the Welsh capital, locally sourcing resources and a supply chain was a crucial focus for ISG. A target of 70 per cent of both was set to ensure the project both benefited and reflected the city.
Delivering the project to the highest standard in such a central area also required intense stakeholder engagement. With the Principality Stadium behind the development and Central station directly in front, contractor, stadium and Network Rail were in continuous communication.
“We have to thoroughly co-ordinate, making sure everything is clear for when events are taking place at the stadium and ensuring entrance and exit to the station are not blocked up,” Mr McElroy says. “Dialogue is constant with Network Rail – we hold weekly conversations with them.”