Construction UK Magazine speaks with Paul Cole, Chief Engineer at Skanska about their recent low carbon concrete trial
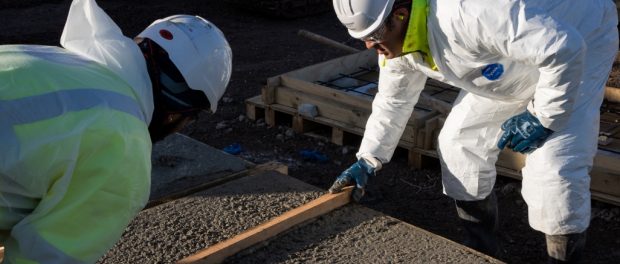
Talk us through the carbon concrete trial and the main aims
This research and innovation project has considered solutions around new concrete technologies to reduce the carbon content of currently used conventional Portland cement concrete and steel reinforcement. We aimed to explore the adoption of low carbon materials for use in reinforced concrete with at least a 50% CO2eq reduction over current conventional practice.
The reduction in capital carbon emissions sits within the National Highways environment and wellbeing designated fund plan and concrete is one of the major sources of capital carbon within infrastructure. This project aimed to focus on reducing this capital carbon, initially for use in temporary works, where design constraints are less onerous, and subsequently within permanent works.
The project aimed to build a better understanding of the use of Basalt Fibre Reinforced Polymer (BFRP) reinforcement in Alkali-Activated Cementitious Material (AACM) concrete to enable widespread, low-risk use for temporary works structures that would inform future use in permanent structures. Further to this, it worked towards the potential adoption of corrosion free reinforcement; addressing the requirement to develop longer lasting materials in construction and reduce maintenance of concrete roads.
Carrying out this trial would enable a better understanding of the impact of the use of these materials ahead of the new Eurocode 2 standards that are currently being drafted to incorporate composite materials.
What were the main factors that needed considering before carrying out the trial
The objective of the trial was to evaluate the performance of a combination of AACM geopolymer concrete and BFRP composite reinforcement for an optimised low-carbon solution. Investigating the performance of this combination of materials through full scale site trails and rigorous laboratory testing would help us develop a better understanding of the of these new materials to enable confident use.
The project was considered to build knowledge of cure, functional properties and structural behaviour. Our benchmark was a traditional reinforced concrete slab using steel mesh in a Portland Cement / GGBS based concrete mix, designed with a similar strength. It was also considered that at the end of its life, the feasibility of recycling through planning, for re-use of the arisings as a graded sub-base type material, should be investigated. Alongside the conventional tests for fresh concrete, test panels and samples were manufactured to test flexural, shear and pull-out performance.
For permanent structures, the benefit of corrosion-free composite reinforcement is well understood and offers a reduced maintenance cost. However, there appears to be uncertainty, gradually being addressed by research, regarding whether AACM geopolymers will inhibit the corrosion of steel reinforcement over time. The use of corrosion free BFRP reinforcement is believed to mitigate this risk. We considered it was necessary to carry out literature study research and document the veracity of the above understanding for steel in AACM geopolymers; this would then be used within comparative Assessment of environmental performance for a typical permanent structure.
It was considered that the success of this innovation project would be measured by the generation of recommendations for further research that would enable other schemes to utilise these materials. The key consideration was that to provide sufficiently robust performance data for this combination of materials to National Highways as a starting point for them to assess their use in their permanent works.
Were there any obstacles/problems?
The greatest problem encountered was with the theoretical design approach for a BFRP reinforced AACM concrete slab.
Initially, it was proposed to design a slab arrangement that comprised
- Ground bearing pavement area
- Bridging section over some notional buried service
Various design standards would be used to provide equivalent designs for the combinations of material. The trial road slabs would be designed to carry 32 tonne 4- axle rigid heavy goods vehicles (HGVs) as a typical load case.
Initially, the slab was modelled as a beam on springs, with the ground represented by spring stiffnesses, to determine the design effects for the slab. From this analyses moment and shear design values were determined.
It was anticipated that the steel reinforced sections would be designed using EC2 and the BFRP reinforced sections using ACI 440-15. It was anticipated that the load factors effects would be reduced from the normally applied values, by the same proportion, in order to cause a higher degree of utilisation in the constructed slabs. The design outputs could be compared to see if there was an equivalence in the proposed designs.
Whilst it was possible to design comparable sections for flexural resistance, shear resistance was more of a problem. The reduced axial stiffness of the FRP reinforcement significantly reduces the concrete shear resistance of those sections. It was found that, unless links were to be added to the design, it was necessary to increase the slab thickness significantly to produce a slab design that could carry the loads on the bridging section. This meant it was no longer feasible to produce directly comparable designs. The thicker slab depths would produce slabs that were sufficiently robust that the differences in the reinforcement selection was not significant.
At this stage it was decided a different approach was required and a ground bearing solution, without a bridging slab, was preferred. The use of a technical report (TR66) was applied to the design. This method provides a simple pavement design for relatively lightly loaded pavement slabs and hard standings. The method provides tabulated designs based on TRL methods. Analytical designs were not produced for equivalent alternative slab constructions. The decision was taken to provide a material ‘like for like’ in that the same depth and strength of concrete was reinforced with the same areas of reinforcement of the two different types.
Observations would evaluate whether a design incorporating the same strength concrete and same area of reinforcement behave in a noticeably different way.
What were the main outcomes of the trial?
Flexure
- The failure mode of all test panels was as expected. The steel reinforced panels failed by yielding of the steel rebar and the BFRP reinforced panels by crushing of concrete in the compression zone.
- All panels carried more than the predicted failure loads.
- The BFRP reinforced panels experienced greater deformation but partially recovered when unloaded. The steel reinforced panels failed by yielding of the steel, as expected, and had no recovery.
- The CIIIA/BFRP mix test panel carried a higher failure load than the AACM/BFRP panel. This may be explained by the CIIIA mix concrete having a higher strength at time of testing than the AACM mix slab.
Shear
- The failure mode of all test panels was as expected.
- The steel reinforced test panels failed at lower loads than predicted.
- The BFRP reinforced panels failed at significantly higher loads than expected.
How vital is it for the industry to reduce carbon?
It is hugely vital that we all drive to reduce carbon. We are awash with statistics surrounding carbon but as a couple of rough figures to put things in perspective, the construction Industry is responsible for approximately a third of energy demand and around a third of process-related CO2 emissions. Furthermore, 4-8% of the worlds CO2 emissions are attributable to the production of concrete, half of which is emitted through the manufacturing process of cement clinker. Something can be done about this and we have a responsibility as leaders in our industry to act.
What will the next stages entail?
Our trial produced a long list of areas requiring further work. Too many to list here. However, in direct reference to the two main materials being trialled the suggested areas for further work are as follows.
The trials have highlighted a number of areas for further consideration when conducting live trials on AACM concrete.
- Effect of ambient temperature, -5˚C to +30˚C
- Early life surface abrasion
- Surface damage due to rainfall during placement
- Freeze thaw resistance
- GGBS Characterisation and link to early strength gain / maturity curve
- Taking samples and/or testing to assess long term durability
- Use of AACMs in Cement Bound Granular Material (CBGM) and Roller Compacted Concrete (RCC)
Based on experimental work with BFRP and work with industry on its properties and characteristics, a number of key areas have been summarised for further research:
- Identification of lower carbon footprint resins
- Research into fibre optic sensors (For use in smart bars, structural health monitoring etc)
- The automation and upscaling of BFRP reinforcement and mesh production
- Comparison of sand coated bar with bar with spiral windings particularly with regard to pull-out test performance
- Pull out tests with varying reinforcement diameters and embedment depths
Other materials also need to be considered in this field. Graphene, Limestone and Clay to name a few.
One product (Concretene) although in very early stages of development, when added in very small quantities to a concrete mix, does exhibit promising properties worthy of detailed further assessment. The product is also storage stable.
Further work could include targeted graphene trials to consider various concrete properties, workability, live time (the time fresh concrete remains workable) and ease of pumping.
Portland Limestone Ternary cements (BS EN 197-5) – lower carbon footprint
- These products are likely to be included and published in BS8500 by Q2 2023
Calcined clay
- As a replacement for GGBS in the future.