Wessex Garage Doors: Repair or Replace for Property Portfolios?
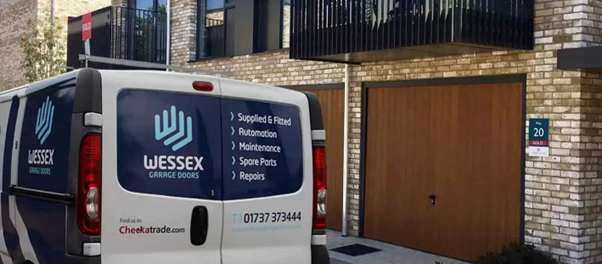
Sponsored by Wessex Garage Doors, this guide offers developers and investors strategic advice on whether to repair or replace garage doors within their property portfolios. As a leading provider and installer of garage doors across the South East for over 30 years, Wessex Garage Doors’ extensive experience in diverse installations and planned preventative maintenance establishes them as an authority on the longevity and security of these crucial components.
For developers and investors, deciding whether to repair or replace a garage door is a decision that can impact budgets, security, and the overall property value. Wessex Garage Doors advises a strategic approach, emphasising that while cost-effective repairs can extend the life of a functional door, a full replacement can be necessary when faced with significant structural damage, escalating maintenance costs, or looking to switch to automation for convenience.
The strategic importance of long-term planning
Short-sighted specifications can cost developers and property managers significantly more in the long run. When initial procurement decisions prioritise the lowest upfront cost over a material or product’s lifecycle value, the consequences ripple through years of ownership. Cheap doors will often require frequent repairs, suffer premature failure, and create ongoing maintenance headaches that erode profit margins and tenant satisfaction.
Then there’s how often the doors will be used. In a residential setting, they might face daily use while in a commercial property, you’ll need robust solutions that are capable of withstanding intensive use patterns while still maintaining professional appearances.
The foundations of durability
Climates form the cornerstone of garage door longevity, especially where materials are concerned. The British weather’s combination of persistent moisture, temperature fluctuations, and exposure to coastal salt creates challenging conditions for any building’s structure.
While steel doors may be considered the most durable option, in certain climates they might require galvanisation and powder coating to resist corrosion, while aluminium options offer natural corrosion resistance but demand careful attention to temperature fluctuations. Timber doors, though aesthetically appealing, need regular staining and treatment to withstand moisture ingress.
The quality of the door’s components should also be checked for reliable performance and safety measures. Springs are perhaps the most critical element, with torsion springs generally offering superior longevity compared to extension alternatives. Quality torsion springs, properly specified for the weight of the door and its usage patterns, typically deliver 10,000 to 20,000 operating cycles before requiring replacement, while inferior components could fail within 5,000 cycles. Rollers, hinges, and cables should also incorporate heavy-duty, corrosion-resistant materials to prevent premature wear.
Check that your chosen door has been approved with the relevant certifications including CE marking for European compliance. Products meeting British Standards, particularly BS EN 13241 for industrial, commercial, and garage doors, ensures compliance with safety regulations and provides performance benchmarks.
Insulation and weather sealing will significantly impact both energy efficiency and your door’s longevity. Properly insulated doors reduce thermal bridging effects that can cause condensation problems within the door structure, while effective sealing systems protect internal mechanisms from environmental degradation.
You also need to ensure the door is integrated properly with the building envelope, paying careful attention to flashing, drainage, and weatherproofing details around the door opening. Poor integration allows water to infiltrate the door and will degrade door components, requiring expensive remedial work.
The dangers of poor installation
How well your garage door has been installed will fundamentally determine its performance, regardless of how high-quality the door itself. Misalignment, incorrect spring tensioning, and inadequate fixing methods all accelerate wear patterns, create safety hazards, and even potentially void manufacturer warranties. These defects tend to manifest as irregular operation, excessive noise, premature component failure, and potential safety risks that expose property owners to liability concerns.
Professional installers understand the importance of checking building tolerances, accommodating thermal movement, and ensuring adequate clearances for smooth operation. They also recognise the significance of safety testing procedures.
Establishing a PPM schedule
Planned preventative maintenance (PPM) programmes need to be tailored to each property to include unique environmental conditions and how frequently the door is used. Commercial installations will typically demand more frequent attention compared to residential properties, for example, while coastal locations necessitate enhanced corrosion protection measures.
Weekly user checks form the foundation of effective maintenance programmes. These simple maintenance checks should include a visual inspection for obvious damage, listening for unusual operational noises, and verifying that the door is operating safely.
Quarterly or biannual professional servicing is also valuable. They’ll be able to provide a comprehensive evaluation including lubrication, tension adjustments, safety checks, and an assessment of individual components. These scheduled interventions typically prove far more cost-effective than reactive maintenance approaches that address failures after they occur.
Sustainable solutions
Deciding whether to repair versus replace will naturally require cost analysis, but it’s also important to look at the sustainability factor too. Investors and developers should look at whether their disposal and recycling practices align with construction waste regulations, and if they are supporting wider environmental responsibility goals.
Steel panels, aluminium frames, and hardware typically offer good recycling value through established scrap metal networks, while wooden doors might be valuable for biomass energy production. Many manufacturers also now offer take-back schemes or partner with specialist disposal contractors to ensure responsible end-of-life management.
Generally speaking, repairs prove economical when it comes to addressing isolated failures on otherwise sound door systems. However, we’d recommend looking into replacements when you’re faced with multiple component failures or your door can’t accommodate the necessary security or automation upgrades. Whichever option you choose, be sure to do your research into the right materials, style of door, and security measures to ensure your garage door is suitable for your property.