Unreliable mobile coverage poses serious operational and safety concerns in Smart Construction and Industry 4.0
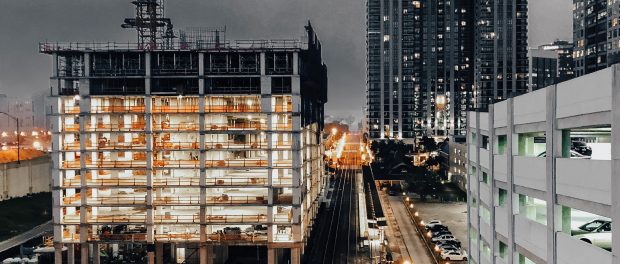
“IoT driven processes along with predictive maintenance and proactive monitoring technologies are reliant on cellular connectivity for reliable and safe operability,” says Gearoid Collins of Vilicom”
For an industry that accounts for 6% GDP worldwide, construction players have been slower than most to embrace IoT. However, the rising impact of construction technologies has opened new doors for digital transformation across the sector and is changing the face of the industry. As such demand for embedded tech, automated access control, CCTV, self-guiding vehicles, connected conveyor systems and a wealth of intelligent machines capable of performing complex tasks independent of human involvement is at an all-time high.
No longer limited to sci-fi, these autonomous technologies have already shown their true worth in industry and manufacturing. The construction industry is also rapidly realising the power of automation as researchers continue to explore how interconnected machines can be used to cost effectively overcome complex structural engineering challenges. What’s more, their usage is set to accelerate in the aftermath of the pandemic and the ongoing consequences of Brexit which have resulted in a much-diminished workforce. Construction robots can significantly speed up repetitive building tasks, increase efficiency through side-by-side deployment with real-world people and dramatically reduce the risk of injury when working at height.
If Covid-19 and Brexit weren’t enough to contend with, the industry is also experiencing global supply chain issues, and as such construction firms are under heightened pressure to work smarter by making greater use of cloud-based technologies like building information models (BIM) and connected site software platforms for greater visibility and insight. Digitized processes and applications are needed, not only to keep costs down and to reduce unnecessary close contact in confined spaces, but to futureproof the industry against other major upheavals or unforeseen scenarios.
From construction sites to production lines
Not only are construction companies having to come to terms with new working practices post-pandemic, prefabricated building modules and 3D printing are driving change in the industry by transforming building sites heavily reliant on a manual labour force into fast paced production lines powered by IoT.
However, whilst IoT and automation is accelerating the assembly of these modular buildings, the construction robots, in some instances, are proving to be counterproductive because of their “more haste less speed tactics”, which can compromise health and safety. State of the art assembly lines controlled by inexhaustible machines are driving up fulfilment targets, with labourers struggling to source the required brackets/parts/subframes in time with such slick operations. If these Smart production lines are to operate in accordance with current standards, the associated maintenance and damage detection processes must also be automated to ensure the smooth running of the interconnected machinery/equipment to minimise risk and maintain a safe working environment.
And the larger the site, the more important this becomes. Large Inner-city projects, comprise an abundance of cutting-edge machinery such as AGVs (automated guided vehicle systems) drones or automated scaffolding systems. If said scaffolding, for example, were to be pushed out of line, causing a machine failure, structural collapse or injury, the cost in lost time or equipment damage is serious in itself, but the potential for large compensation claims is enormous.
Cellular connectivity is integral to machine safety
Whist it’s encouraging that building companies are embracing IoT and automation, few industries encounter as many comms challenges as the construction one. Large scale building projects typically involve extreme locations – offshore, subterranean, – both of which are off grid, or densely populated areas surrounded by connectivity obstructions such as tall buildings. To exacerbate the situation, their comms requirements are not only demanding, with hundreds of devices and machines to power, they are constantly moving goal posts. What is deemed sufficient one week quickly becomes obsolete as the project advances and building exteriors are filled mobile blocking materials like reinforced concrete, steel, and glass.
Apart from causing a commercial inconvenience and posing serious health and safety concerns, lack of a mobile signal source is detrimental to M2M communications. The obligatory maintenance and support systems pivotal to sustained equipment and staff safety in smart construction setups are unable to trigger an incident without cellular coverage because the service used is SMS. Mobile connectivity is used because it’s readily accessible, it’s cheap, and, with encryption, it’s secure.
Ensuring reliable coverage is no mean feat
With all these considerations to take care of, the deployed comms infrastructures must be able to support existing devices and services as well as high performance low latency connectivity needed for IoT and automation to facilitate interconnectivity and assure people and machine safety. And all this must be achieved cost effectively and with minimal disruption to the project. A robust private mobile network capable of supporting thousands of devices and applications simultaneously is needed.
As smart technologies go mainstream 5G is poised to become the underpinning enabler to digitization and IoT but the widescale rollout of this next generation network is still a long way off due to the infrastructure overhauls needed at carrier level to support cloud computing and data backhaul. In the meantime, the health and safety systems operating alongside smart machines still need a reliable trigger mechanism and for the foreseeable future this will continue to be cellular.