Moxon and Mott MacDonald unveil prototype for Overhead Line Structure
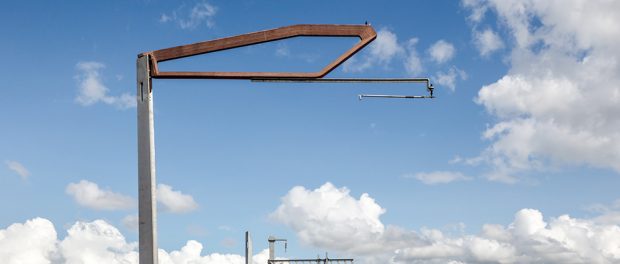
Moxon and Mott MacDonald have unveiled their prototype for a cost effective, low maintenance and visually sensitive alternative to the overhead line structures currently used for conventional and high-speed rail projects.
The integrated overhead line equipment structure (OLS) combines the structural and electrical protection requirements into a single component, allowing the new design to reduce the height and visual clutter normally associated with overhead line structures. The patent pending design achieves this through the use of a densified wood laminate in the cantilever arm. Exceptional structural and electrical insulating properties work together in a material that lends itself to being machined to a high degree of precision.
Benefits of the innovative system include:
- Reduced visual impact due to overall height being 25% shorter than existing typical OLS systems, easing statutory consents, particularly in visually sensitive locations.
- Innovative use of wood to provide a distinctive, attractive cantilever.
- Reduced installation time as the mast and cantilever can be erected together as a single unit from a road-railer or train. Individual units can be erected in just five minutes.
- Complete interoperability with existing OLS systems by utilising standard connections and components already familiar to OLS engineers.
- Light-weight components help with ease of installation and can be neatly stacked for transportation and storage.
- Maintenance is simplified through a 70% reduction in number of components, reducing remedial engineering time and thus limiting impact on services.
- 32% saving in embodied carbon compared to typical alternatives.
Ben Addy, Director at Moxon, said: “Railway catenary systems can have an enormous effect on the appearance of high speed and conventional railway lines as they pass through the landscape. Our integrated OLS substantially reduces the visual impact of these systems, allowing them to sit more harmoniously within their environment. However, at a time when efficiency and service performance of our railways is under huge public scrutiny, it is important the strength of our design goes far beyond aesthetics. Our system features complete interoperability with existing OLS systems, ensuring ease of installation and no need for additional engineer training. Similarly, by significantly reducing the number of components, we have reduced the routine maintenance time needed for each unit. These immediate and long-term efficiencies and cost-savings make our integrated OLS a commercially compelling alternative to other systems currently available.”
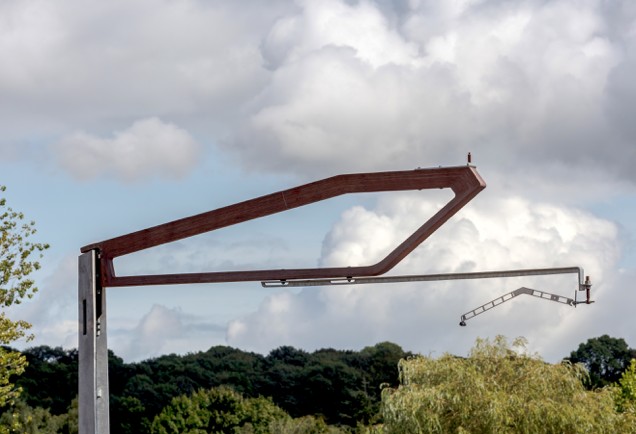
Moxon Integrated OLS Prototype
Brian Duguid, Director at Mott MacDonald, commented: “Our integrated OLS system has been designed to be fully compatible with existing, proven overhead catenary hardware for both conventional and high-speed railways, including HS2 in the UK. The design development has created a structure which is quick and simple to erect and able to achieve high installation rates. We have successfully completed two full-scale prototypes to confirm the system’s practicality and look forward to working with interested partners to introduce it onto working railway systems.”
The prototype has been in development since 2014 and was selected as one of three finalists in a 2014 RIBA design competition commissioned by FutureRailway, finishing above more than 60 similar schemes from 14 countries. As a result, Moxon and Mott MacDonald received £150,000 to further develop the system, focusing on technical and analytical modelling and its route to market.
By exploiting densified wood laminate’s intrinsic electrical insulation properties, conductors and supply cables can be fixed directly onto the structural arm without the need for bulky and visibly obtrusive ceramic insulating pots. This integrated approach enables the dramatic reduction in the size, complexity and number of connections while simultaneously encouraging a previously unseen degree of structural and aesthetic freedom in terms of the size and shape of the cantilever.
Slender engineered bracketry connects proven OLS registration and catenary hardware to the new mast with the high range of dimensional flexibility that is critical for railway applications.
A low-profile adjustable hinge arrangement permits vertical adjustment where the cantilever arm connects to the mast, allowing tolerance in the foundation position and overall height in line with that found in existing OLS cantilever structures.
The tapering vertical steel mast has a pronounced ‘V’ form in plan section. Tapering inwards towards the top makes for an efficient use of material as the cross section reduces with the bending stresses. The point of the mast’s ‘V’ shape faces outwards away from the track-side – further reducing the visual complexity of the mast. The void between the faces of the ‘V’ enables discrete positioning of secondary components and fixings within the overall form of the structure without impacting upon the silhouette.