World’s strongest land-based crane passes test program
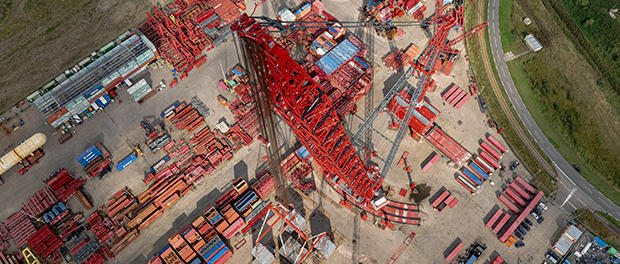
Mammoet has officially completed testing of the SK6000 – the world’s strongest land-based crane. This process – overseen by maritime classification services organization Lloyd’s Register, certifies the crane’s safe operation to its specification.
After reviewing the SK6000’s engineering design earlier during its development, Lloyd’s Register confirmed that the test program was suitable to prove out its capacity charts. Testing was then carried out at Mammoet’s Westdorpe facility in the Netherlands over the last three months.
A comprehensive functional test program confirmed the crane operated to its specification, and to the strictest safety levels.
Next followed structural and stability testing, during which the SK6000 was subjected to a range of lift weights and conditions, proving that all components withstand 125% overload.
These tests covered the maximum extents of all load charts for the crane, for all main mast configurations, from shortest (127m) to longest (171m).
At its most strenuous, this process tested the crane to a maximum load moment of 520,000 tonne meters. This is well over one and a half times greater than the rated load moment of the SK350 – which was previously the world’s strongest land-based crane.
The SK6000 helps Mammoet’s customers across the energy sector to build on a larger scale than ever before, using modularized construction techniques to build in parallel and enhance the efficiency of assembly phases.
As offshore wind components grow to reach stronger wind flows, the SK6000 ensures the future constructability of today’s planned wind farms. As the market develops, and lifting to heights beyond 171m is required, its jib can be fitted to enable lifts of 3,000t to 220 meters.
In the nuclear sector, the SK6000 reduces on-site construction time and increases safety by allowing larger mass components to be constructed in controlled conditions and assembled quickly.
In oil and gas, its huge capacity and outreach allows maintenance and upgrade projects to take place with reduced disruption, and new-build projects to deliver economies of scale from FEED to installation – and beyond.
The SK6000 will now be boomed down and containerized, ready for shipping to its first project in early 2025.