Willmott Dixon’s new Passivhaus school aims to cut energy use by 80 per cent
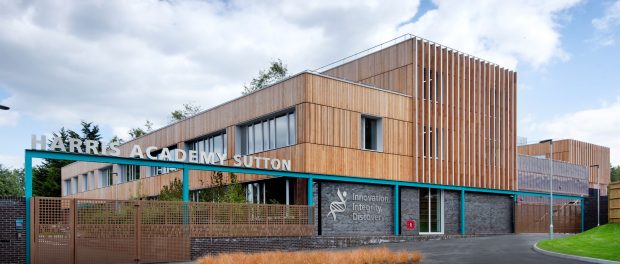
Pupils and teachers at the UK’s first Passivhaus secondary school will enjoy a swathe of benefits in the quality of their new teaching environment.
By adopting Passivhaus, Harris Academy Sutton in South London will deliver energy consumption that’s typically 80% lower than a standard new school building, while providing better air quality and the right amount of natural light to create an optimum building environment to study and work in.
Constructed for the London Borough of Sutton by Willmott Dixon, the six-form entry school completed for the start of the 2019/20 academic year accommodates 1,275 pupils and 95 staff. It forms part of Sutton’s masterplan for the London Cancer Hub – a major project to create a world-leading life-science campus for research, treatment, education and enterprise.
Throughout the year, mechanical ventilation (with heat recovery) will provide fresh air, with the quantity locally adjusted in response to CO2 level sensors in all the rooms. In the winter, fresh warm air heats rooms and spaces. They never get stuffy, which tends to cause sleepiness, and there are no uncomfortable draughts or cold spots.
In the summer, the building stays fresh and cool. As a result, pupils and staff feel alert and comfortable all year round, which positively impacts learning ability, wellbeing and teaching quality.
The Passivhaus ‘fabric first’ approach is about carefully optimising the fabric of the building itself so that energy efficiency is achieved passively. It centres on measures such as extra thick insulation in walls, floors and roof; triple glazing on windows and doors; and an exceptionally airtight building envelope – approximately 14 times more airtight than building regulations require.
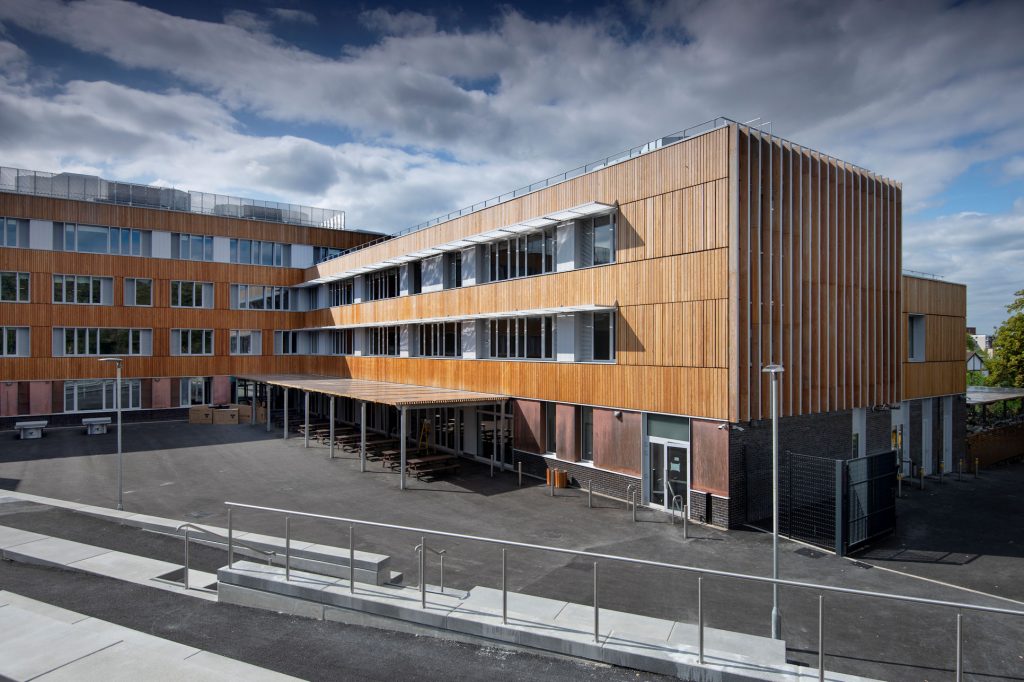
Collaboration
From a very early stage, Willmott Dixon worked with Architype, expert Passivhaus architects, as a single partnership team with a common goal. This one-team ethos enabled construction expertise to inform design and vice versa, and meant that challenges could be solved effectively to make sure of the best and most cost-efficient delivery.
Close collaborative working continued throughout the entire build period. This included regular site meetings and brainstorming sessions to find solutions to design details that were difficult to put into practice, and joint involvement in ensuring quality on site.
“For all of us, this was very much a co-operative, partnering process,” said Adam Whiteley, Senior Project Manager, London Borough of Sutton. “As the project evolved, everyone demonstrated these values in a very positive way.”
Construction
Passivhaus buildings have more high-performance elements and the specification for mechanical and electrical components requires better products. In addition, contractors need to be extremely diligent to ensure the top quality workmanship and installation that the standard requires.
With quality critical to achieving certification, Willmott Dixon engaged with the supply chain at a very early stage to communicate its significance, and continually reinforced the importance of getting things absolutely right. Graham Thompson at Willmott Dixon explains, “A key part of this was a Passivhaus-specific induction for the entire supply chain. Every person was made aware of the concept, why getting everything right was so important and why stringent quality control was essential.”
To support this, an open, ‘no blame’ culture was established, with everyone encouraged to speak up if they thought something was being done wrong. These messages were strengthened by toolbox talks throughout the project and by having posters on constant display.
Very high levels of insulation are integral to Passivhaus. Where insulation boards abut there must be no gap, additionally the tolerance (air gap) behind and between can be no bigger than 3mm so quality needs to be outstanding. For example, the school’s ground floor, set on concrete slabs, and CLT roof both required perfectly abutted insulation boards that met these extremely tight gap tolerances, through multiple layers with staggered joints. On the timber-framed second and third storeys, insulation was pumped into the wall void to completely fill it.
Achieving airtightness is a huge challenge on a Passivhaus building and it can’t be left until the end of a project. Every single interface needs to be completed efficiently and to high quality standards, every inch of the airtightness membrane needs to be checked, and checks and tests must to be carried out continually.
Rigorous control of any type of drilling or penetration through the building envelope is essential. On the project, penetration schedules were set, with every item carefully inspected to make sure it was correctly sealed and signed off before being covered over. As part of the process, two Willmott Dixon airtightness champions were appointed. They continually checked every area and made sure that penetrations were fully and correctly sealed, and took photos of everything for compliance submissions to the Passivhaus accreditation body.
On a Passivhaus building, the requirement is for very low air leakage rates, with no more than 0.6 air changes per hour. For conventional buildings, the air change requirement under building regulations is around 10.0 m3/h.m2 and for a BREEAM building, it’s 4.0. Willmott Dixon achieved 0.30 air changes per hour on the school (equivalent to 0.7 m3/h.m2), which for a building of over 10,000 square metres is remarkable.
“The airtightness champions were instrumental in achieving the building’s low air changes per hour”, saidChristian Dimbleby, Architype Architects. “They carried out constant checks all around the building for about two years, which really shows their commitment”.
Key outcomes
• Very low operating costs
• Very low carbon footprint
• 80% less energy use than a conventional building
• Ideal internal temperature all year round
• Superb air quality for better learning, health and wellbeing
• Exceptional airtightness – around 14 times lower than building regulations
• 0.30 air changes per hour – half the Passivhaus 0.6 requirement
• 40% project spend with local business