Three Months or Less? Strategies to Maximize Equipment Lifespans in Harsh Mining Conditions
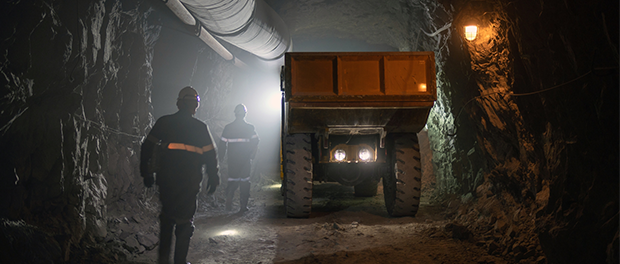
How long can a new front-end loader last in a limestone mine? Just three months would not be a wrong answer, given the corrosive atmosphere present one mile underground. Unfortunately for mining companies, equipment equals money, and replacing assets that cost hundreds of thousands of dollars every few months is not an economical option. Moreover, heavy equipment is not the only victim as corrosion eats through any metal in its path—from electricals to lunch boxes. While it is impossible to completely stop corrosion, it is possible to slow it down and start minimizing the consequences immediately with several handy maintenance options from Cortec® Corporation.
Loosen the Hold of Existing Rust
One of the challenges of rust is that it can lock moving parts, such as nuts, bolts, and hinges, into place, making it difficult to impossible to do maintenance. VpCI® Super Penetrant allows miners to quickly penetrate through deep rust and loosen frozen parts so that they can move freely. This is such a lifesaver in a corrosive mining environment that one limestone mine started using a can on Friday and it was gone by Monday, prompting them to order an entire caseload of VpCI® Super Penetrant.
Start Protecting Electricals
Electrical wiring and boxes in underground offices and throughout the mine are also vulnerable. One easy way to slow down the corrosion process is by placing VpCI®-105 or 111 Emitters inside electrical panels. These self-stick cups release corrosion inhibiting vapors through a breathable membrane, conditioning the enclosure with chemistry that forms a protective molecular layer on metal surfaces such as electrical contacts. Exposed wires and contact points can be sprayed with ElectriCorr™ VpCI®-239 to clean away existing corrosion products and/or to leave behind a thin protective layer.
Extend Equipment Service Life
If a mining truck has already spent three months underground, it may be too late to undo the corrosion damage. However, if only a little surface rust has formed, CorrVerter® Rust Converter Primer can be used (along with good surface prep) to passivate and slow it down. With the high frequency of truck replacements, it is likely that miners will also see new equipment before long.
The day the equipment arrives is the ideal time to perform preventative corrosion maintenance by fortifying each truck with an extra layer of protection. This can be done with a water-based anticorrosion acrylic topcoat such as EcoShield® VpCI®-386. Epoxy and urethane coatings that provide greater hardness are also available for additional mechanical protection against the heavy wear and tear of a mining environment. Unpainted metal surfaces in some cases may be protected with a layer of VpCI®-368, a tough waxlike film for stationary surfaces, or VpCI®-369, a wet film for moving parts (these two coatings are also available in aerosol spray can versions under the CorShield® brand for application convenience). Since abrasion can wear away the coatings over time, it is important for maintenance crews to perform periodic inspection and coating touchup as needed. This is a small investment compared to the cost of replacing a truck.
Take the Time to Slow Corrosion
Corrosion is an aggressive force in underground mines. While it seems unstoppable, there are a variety of ways to slow it down and diminish the negative effects on mining assets. If you need support analyzing your trouble points and tailoring a corrosion mitigation plan, don’t hesitate to reach out to Cortec® for assistance.