The Critical Need for Reliability in Construction Project Planning
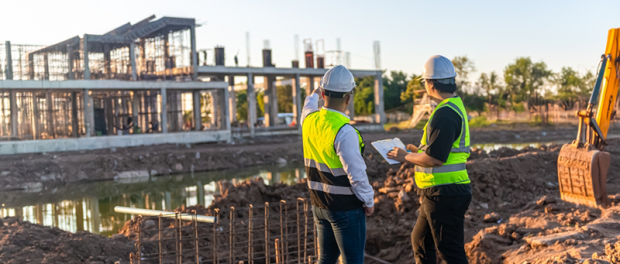
By Mark Chapman Elecosoft
Putting together a reliable plan for how a construction project is going to be delivered is exceedingly hard – and it’s getting harder.
Projects are not only getting bigger and more complex, there are more stakeholders involved, often with divergent agendas. Construction projects of the past used to be far more straightforward than their modern counterparts. Various constraints, including sustainability concerns and regulatory requirements, to name just two, create a path littered with obstacles. Plus, it’s no longer acceptable to build a project of any kind without considering how it integrates with existing infrastructures. Add in “optimism bias”, where initial project estimates are overly unrealistic, and you have heightened the complexity exponentially.
Yet, despite widespread dissatisfaction when projects run late, take longer than expected, or encounter unforeseen issues, the industry seems reluctant to tackle the root causes of unreliable planning head-on. In fact, given these critical issues, along with numerous others, it’s easy to see that the concept of reliability is not given the attention it deserves right from the start. Despite the usual litany of project meetings and forecasts, this glaring issue remains unchanged.
Before diving into the reasons behind the deterioration of reliability, let’s define the word “reliability” in the context of the construction sector. According to the American Society for Quality, reliability is defined as “the probability that a product, system, or service will perform its intended function adequately for a specified period of time or will operate in a defined environment without failure.” Using this definition in our context, it means that the construction planning process will ultimately result in a project that is “on time, on budget, and matches the agreed-upon standards of quality.”
It should be noted that this quest for reliability should extend not only to the project schedule but the larger construction plan. The schedule is a detailed timeline specifying when different tasks or phases of a project will start and finish; the plan is a comprehensive document or strategy outlining how the construction project will be executed, including scope, resources, methodologies, and strategies for completing the project. Still, the schedule’s importance should not be minimized, as it is arguably the most critical element of the greater project plan.
Progress Over Reliability
One of the most obvious hindrances to attaining reliability is that the construction industry has become overly fixated on progress tracking rather than ensuring the reliability of the initial plan. Case in point: Project management offices (PMO), as well as the broader project controls industry, have developed myriad tools to track hours and days lost – even minutes. However, these tools focus primarily on short-term metrics, neglecting the importance of establishing a reliable plan from the outset. By focusing so intently on short-term thinking, the need for long-term planning and dependable delivery strategies is often ignored. Quite often, the detailed calculations of how long tasks will take do not hold up under scrutiny, and delivery strategies fail to align with the overall program. Progress without reliability is a hollow victory.
Related to this is the practice of relying on historical progress as an indicator of future performance which is not nearly as useful as forecasting reliability. The current preoccupation with tracking past performance, while somewhat helpful as a reference point, does little to improve future outcomes. Instead, emphasis must be placed on ensuring that initial and ongoing plans are realistic and achievable. This requires the industry to embrace a cultural shift, with reliability prioritized from the start and continuously monitored throughout the project lifecycle.
At its core, planning is a team sport, requiring the participation of multiple parties, all contributing to the greater objective. Thus, those tools that support collaboration and innovation are critical for creating reliable plans. But if, as an industry, we have an endemic problem with cost and time overruns, then why are we locking down how they are managed and not actively encouraging and rewarding innovation in these two critical processes?
Tools of Choice
A major obstacle to achieving reliability – particularly in the US, UK, and Australia – is the current practice of allowing the client or project owner to specify both the process and the tool to be used in the planning process. You wouldn’t tell a carpenter which hammer they should use; why should construction planning be any different? In fact, they not only specify the tools to be used but also how work should be broken down, and the metrics for measuring progress. This rigid approach, often centered around traditional, “brand name” tools, falls short.
Why is this a mistake? Because a substantial percentage of the primary planning tools used in construction were either designed for other industries or for general-purpose use. Besides lacking proper functionality, they fail to facilitate or encourage the necessary innovation in the planning process. Consequently, they become tools accessed by a small group in isolation; the rest of the project team, meanwhile, remains disengaged. The preferred approach is for clients to focus on the desired data outcomes and give contractors the freedom to determine the best methods for achieving those outcomes. This approach promotes innovation and leverages the expertise of construction professionals to deliver more reliable projects. It makes no sense to force a contractor to rely on a project planning tool they are not comfortable using.
There are tools that are designed specifically for the construction industry, allowing for better communication and understanding among project stakeholders. They help foster a collaborative environment essential for successful project delivery. Once the client or project owner has chosen the best contractor for the job, they should allow the contractor to dictate their choice of planning tools; doing otherwise can throw a wrench into the entire project.
Long-Term Thinking, Lifecycle Considerations
No one would argue that decisions made during the planning and design phases have long-term implications for a project’s operational and maintenance phases. The sad reality is that the consequences of not paying enough attention to reliability isn’t realized until many years later. If, for example, someone is making poor decisions during the concept design stage, the effect of those decisions won’t be realized until sometime during construction, making it much more difficult to take corrective action. Consequently, construction projects need to be seen within the context of their entire lifecycle, from concept to decommissioning. By involving operational expertise at the inception of planning, the industry can create plans that are not only reliable but also sustainable and efficient over the project’s lifespan.
Incentivizing stakeholders based on the project’s overall success, rather than their individual contributions, can also foster a more integrated approach to project planning and delivery. This requires a fundamental shift in how projects are contracted and managed, moving away from short-term gains toward long-term value creation. Exacerbating this situation is the current practice of awarding contracts to the lowest bidder – a practice which reinforces the “race to the bottom” mentality that prioritizes cost over reliability and quality, resulting in projects that are prone to delays and cost overruns. Instead, the industry should focus on selecting contractors based on their ability to deliver reliable plans and innovative solutions, even if their initial bid is not the lowest.
Another area where long-term thinking in the construction comes up short is the distribution of risk. Traditional contractual relationships often place an undue burden on contractors, leading to financial strain and, in some cases, business failure. A more balanced approach, where risk is shared openly between clients and contractors, is needed. This approach encourages collaborative problem-solving and ensures that both parties are invested in the successful delivery of the project.
The Human Impact
While the technical and financial ramifications of the reliability dilemma are evident, the human impact should not be overlooked. Poor planning leads to longer hours, high stress, and job insecurity for everyone in the construction pipeline: executives, planners, program managers, schedulers and, of course, onsite workers. Many stakeholders will suffer mental health issues, strained relationships, and a poor work-life balance as a result. With a more reliable and sustainable approach to project planning, the well-being of the industry’s workforce can be preserved.
There is a critical need to amplify the voices of those who understand and advocate for reliability in project planning. These individuals often face resistance from those whose roles are tied to traditional methods and tools. To drive meaningful change, the industry must create a platform for these voices and promote the adoption of innovative planning processes. Further, those who are championing reliability must have the freedom to challenge a project’s constraints and requirements. They should be encouraged, when necessary, to go to the source of the constraint and question why it was created. The truth is, constraints can be old and wrong or no longer relevant.
While it’s impractical or unnecessary to challenge every constraint or requirement, accepting them all at face value begins to short-circuit an individual’s innovative wiring. Imaginative approaches give way to rote tasks, stifling the creativity that will help propel the industry forward while making reliability a far more achievable goal.