Polymeric emulsions and the barriers to getting more traction in the UK
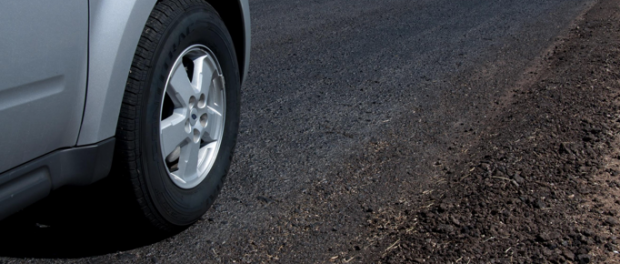
Why aren’t polymers more widely used in paving?
Is the reason environmental? With so much in the news about the damage that plastic is causing to our oceans and the marine life that lives there, it is tempting to write off all polymeric substances as a nuisance. When plastic was pioneered, with so many applications in both the household and industry, it was hailed as a miracle material due its seeming indestructibility. However, it is now undisputed by the scientific and environmental communities that plastic’s greatest strength is also its biggest weakness. Construction and infrastructure, however, are sectors in which the use of polymers is entirely appropriate and beneficial to the environment. We don’t need immortal plastic shopping bags, but we do need enduring roads.
How is polymeric paving kinder to the environment?
Roads that require less maintenance, less quarrying and less transportation of aggregate are more environmentally friendly than those that use traditional construction techniques such as bituminous surfaces. Unlike asphalt, polymeric processes are non-heated, which means fewer CO2 emissions into our atmosphere. In fact, when it comes to paving and soil stabilisation, some polymeric substances have the highest green credentials. These highly engineered glues bind aggregate and native soils together, without the use of harmful chemicals and the subsequent leakage of toxic contaminants to the ecosystem.
After hurricane Katrina, lots of small lumps of bitumen were dumped indiscriminately all over the beaches of the Gulf of Mexico. This was a major issue for both the native wildlife, as well as for bare-footed tourists exposed to the jagged edges of this micro rubbish spread across the beaches. This is why LANDLOCK Natural Paving, Inc. was certified by the US Department of Fish and Wildlife – the solution that holds the road together and better controls the infrastructure impact after major weather events. With more extreme and random weather predicted, this is worth bearing in mind for Northern Europe. Though perhaps we don’t have as many beach goers.
What is the evidence for durability?
When medicines were being used in Victorian England, heroin and cocaine were widely used to quieten babies and alleviate toothache respectively. However, we didn’t let a lack of knowledge and some bad practitioners stop us from developing and using penicillin. Likewise, in the polymer business, a few cowboys use waste stream by-products to create under-performing or failing surfaces. This has led to questions about durability in general, however, when a polymer is custom-engineered with high levels of virgin, prime ingredients, the strength gains significantly exceed the load bearing capacity of a Portland cement treated material. Of course, in dry climates polymers can be used for dust and erosion control too, as a much longer lasting, and often more environmentally-friendly solution than simply spraying a surface with water. But let’s look at more universal applications – farm to market roads and heavy haul roads:
This rural, gravel road built in Uganda is still going strong 7 years later.
A sub-base stabilised road in Illinois that was built in 2014
Is cost the issue?
Asphalt surfaces have been around for decades, but it is often a prohibitively expensive material. Furthermore, asphalt roads are only as good as the base upon which they sit, and thus considered to be ‘floating’ surface. Once the ever-constant forces of erosion reach the base, it’s only a matter of time before the asphalt begins to see cracking and pot-holing, which then requires costly repairs and maintenance. Polymeric-treated surfaces on the other hand create a root-system that connects the surface to the base, making base failures less likely. This means less cracking, pot-hole, and repair work.
Additionally, when it comes to more heavily trafficked roads in urban settings, polymers can be used to reduce the overall profile of design, and create a better support system for a minimal asphalt cap. This ultimately accomplishes two things – it reduces the total amount of aggregate needed to build, thereby reducing material and transportation costs, and it results in a longer lasting asphalt (wear course) because it eliminates erosion at the base level, thereby reducing maintenance and repair expenses.
Lastly, polymers can be used to recycle failing asphalted surfaces, providing an alternative to the traditional approach of ‘remove and replace’. Again, the less material you have to import or export, the more you can save and the faster you can rebuild. As always, cost savings will vary from location to location and from project to project.
An asphalt recycled & reclaimed surface in Phoenix that was constructed in 2009
Maybe people just don’t like change
Why then, in the UK, are polymers not the first choice when it comes to sub base stabilisation and rural road paving? Given that emulsions are cured more quickly by the sun, Northern Europe may not seem like a suitable region. However, LANDLOCK has proven successful in cooler, less sunny environments. Additionally, after further testing, UV lighting could be used as an alternative to sunlight to harden and bind the surface at a more rapid pace. This curing solution will also better control and manage wet weather conditions.
Perhaps a bigger barrier to successful market entry is that, as with any mature industry, there is a resistance to new technology that could upset the normal way of doing things, and of course upset the established players. This is especially true in the public sector. Risk, whether falsely perceived or real, is an uncomfortable feeling for those charged with building safe and permanent structures. The age and continuing high performance of polymeric stabilised surfaces in the USA and around the world should, however, provide reassurance. For those that do have an eye on the future, there are huge rewards in store, in the shape of avoiding the waste of time, money and the environment that traditional road building techniques are inherently plagued by.
Patrick Bremer is Vice President of Business Development for LANDLOCK® Natural Paving, Inc. and explores the current issues in the waste disposal industry and the innovative developments required for long-term sustainability. LANDLOCK is a global leader in the development of Smarter Infrastructure. LANDLOCK’s proprietary, polymeric emulsions reduce the waste of time, money and the environment commonly associated with traditional construction. Patrick can be reached at patrick@landlocknaturalpaving.com or visit www.landlocknaturalpaving.com.