Modern Methods of Construction and Sustainability
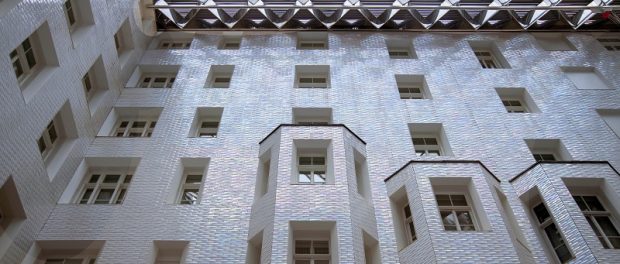
What are modern methods of construction, and are they sustainable enough to meet ESG goals and the Future Homes Standard?
There is no shortage of opportunities for housing developers in the UK, based on the government’s commitment to build 300,000 new homes each year. But, achieving this goal requires a balancing act of somewhat oppositional forces. Crunching timelines and costs is necessary to pass on much-needed affordability to home buyers. At the same time, standards and their enforcement are also increasing, following the Building Safety Act and the upcoming Future Homes Standard.
To simultaneously meet the needs of the market and more robust regulation, the industry requires innovative solutions. One such solution is modern methods of construction. An evolving, complementary approach to traditional manufacture and use of construction products.
What are modern methods of construction?
In traditional manufacturing, producers make individual material units such as clay bricks. These are then transported to the construction site in batches. The contractor installs individual units of the product until the structure is complete. This is the ‘brick-by-brick’ approach.
With modern methods of construction (MMC), some of that construction labour moves further upstream to the manufacturers. Instead of individual units, manufacturers produce pre-fabricated components. These include brick slips and panel systems as well as chimneys, archways or fenestration window details using brick specials. These component build-ups then save time and energy use on-site. In turn, this can reduce costs and embodied carbon emissions.
MMC also includes improvements to on-site labour practices. This spans the implementation of building information modelling (BIM) to novel uses of automation and waste reduction processes or methodologies.
Some might suggest that MMC is set to replace traditional construction, particularly due to the time and costs it can save on-site. However, many projects still need a degree of design flexibility that MMC approaches alone can’t facilitate. Durability and adaptability of materials and design are also key considerations for building in the UK’s variable climate. As a result, a hybrid approach that combines MMC with traditional construction will produce the best outcomes for most projects.
Are modern methods of construction sustainable?
Employing MMC in projects is an effective way to reduce build timelines. Subsequently, this reduces on-site labour costs. But, MMC can also help developers meet ESG goals and the Future Homes Standard. Let’s look at how.
Reducing waste
One of the challenges to employing MMC is that you must finalise more of the design upfront. But, this can also help reduce waste through more accurate product orders. Using BIM in the design of projects improves order accuracy further. And, it helps to ensure that architects and developers are implementing products correctly to meet safety and sustainability standards. This is made possible by the extensive technical and manufacturing data attached to each product’s BIM files, technical data sheets, declarations of performance (DOPs) or product passports.
Lowering carbon emissions
In the built environment, embodied carbon refers to the carbon emissions associated with the manufacture of building products and on-site construction. In one UK study, researchers found that using MMC can cut embodied carbon of construction projects by up to 54%.
Several factors contribute to this, primarily relating to transportation and time required on-site. Larger, pre-fabricated components require fewer deliveries to site, which research in the US demonstrated led to a 60% reduction in CO2 emissions. This US research also highlighted that offsite construction reduces the overall length of on-site construction time. In turn, this reduces the length of time that contractors need to employ plant machinery and workers on-site. Both of these elements rely largely on fossil fuels for transportation, operation and welfare (via accommodation and catering services for workers). So, reducing their time on-site minimises their contributions to embodied carbon.
Manufacturer selection can also influence a project’s embodied carbon. At Michelmersh, we continue to invest in new practices and innovative projects like HyBrick to reduce the carbon emissions associated with the production of clay products. By working with a specific manufacturer that can demonstrate its sustainability credentials, you can further control your project’s embodied carbon.
Ensuring energy efficiency
The Future Homes Standard will become mandatory in 2025. You can control factors such as airtightness and continuity of insulation more consistently in the manufacturing process of MMC façade system products. What’s more, use of BIM can support developers in their Standard Assessment Procedure (SAP) at the design stage. This is due to the precise level of product data and the growing demand for energy efficiency information associated with individual products in BIM files.
The role of clay brick in modern methods of construction
MMC involves a wide range of materials that include timber, concrete, steel and clay brick. Developers can use brick slips and slip panel systems to deliver high-quality projects in shorter timeframes. These faster building solutions still meet rigorous safety requirements and the Future Homes Standard. This is due to clay brick’s thermal performance and non-combustibility. Combined with the relatively short lead-in time for hand-laid clay bricks, projects that use both traditional and modern methods of construction with clay brick can expect faster and more sustainable outcomes. The Ronald McDonald House in Lambeth is just one example we have at Michelmersh that demonstrates the benefits of a hybrid approach, with the project achieving a BREEAM rating of ‘Excellent’.
We’re proud of the consistent reputation for high quality that our products have earned across a wide variety of construction archetypes and projects. But, we’re also here to support the built environment ecosystem. Particularly as it faces the challenges and opportunities presented by increased regulation and environmental shifts.
Visit the Michelmersh News page to read more about important industry topics and company updates.