A practical approach to structural isolation
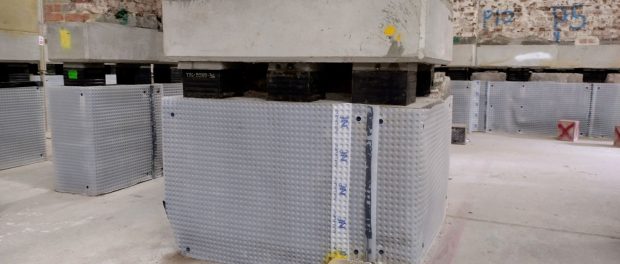
The future of urban development rests on rubber bearings
As urban expansion continues alongside a rise in mixed-used buildings, the need for effective building isolation is growing, especially for structures in close proximity to rail systems and highways. Here, Adam Fox, director at structural isolation specialist Mason UK, offers guidance to architects, developers, structural engineers and acousticians who are working with isolation bearings.
The importance of eliminating perceptible vibrations and re-radiated noise is a critical concern for developers and design teams alike. With more than sixty years of progress in acoustical consultancy and structural isolation, advanced techniques such as low dynamic stiffness (LDS) structural isolation bearing pads have redefined how buildings can be safeguarded against environmental vibrations.
Building isolation is a sophisticated yet essential process that ensures developments remain free of disruptive vibrations. The structural design process incorporates acoustical consultation, engineering precision, and rigorous compliance with building codes to achieve the desired outcome. The effectiveness of these efforts, however, is most vulnerable during the construction phase.
Unexpected short-circuiting of the isolation system, often caused by improper installation or overlooked structural details, can significantly compromise the
intended vibration reduction. Repeated inspections and strategic coordination among architects, engineers, and contractors are critical to ensuring that the isolation system functions as designed.
A collaborative approach
At the core of any successful building isolation project is the collaboration between key stakeholders, including acoustical consultants, structural engineers, architects, and material suppliers. Acoustical consultants initiate the process by analysing the site and determining the levels of perceptible vibrations. Structural engineers and architects then design a cost-effective isolation system that complies with building codes, particularly concerning wind and earthquake loads.
This collaboration has led remarkable transformations, turning marginal properties, such as those previously used for parking garages, into premium commercial and residential developments. With urbanisation growing at a rapid pace, cities worldwide are integrating isolation techniques to enhance building longevity and liveability. A well-designed isolation system not only mitigates vibrations but has a service life longer than the structure it is designed to support, giving you peace of mind in situations where inspection and replacement is practically impossible.
Designing effective isolation systems
The foundation of any successful isolation project lies in designing a system that minimises vibrations while maintaining structural integrity. An essential step in this process is determining the natural frequency of support for the entire structure. This requires structural loadings to be accurately defined to drive bearing compression. Incorporating spring rates into the structural model and reviewing load redistribution
is essential. A uniform natural frequency prevents resonance or vibration amplification that could otherwise arise post-construction. Retrofitting an isolation system is nearly impossible, so it is important to get things right during the initial design phase.
Another key aspect is the selection of the isolation plane. Elevating this plane within the structure helps prevent short-circuiting, ensuring that the isolation system remains effective over time. For example, incorporating car parks below the isolation plane rather than within it prevents unnecessary vibration transmission. To further enhance isolation efficiency, elements such as shear keys and pins play a crucial role. These structural components help manage seismic and wind loads while maintaining isolation effectiveness
The role of bridge bearing pads
Among the most reliable isolation materials are bridge bearing pads, with the best-performing made from natural rubber engineered for low dynamic stiffness. Responsible suppliers should provide independent laboratory testing for these materials to ensure compliance with ISO 9001 and engineering standards such as BS EN 1337, providing developers with a robust and durable solution for structural isolation.
The design of bridge bearing pads is based on shape factor curves and stress-strain relationships, ensuring they remain well below maximum allowable limits. Misconceptions about pad deflection and dynamic stiffness correction factors often lead to errors in implementation. For instance, a 25mm deflection helical steel spring does not have the same natural frequency as a 25mm deflection rubber pad.
Understanding these nuances is essential for achieving the correct level of vibration reduction.
Furthermore, the concept of low stress, low strain design philosophy ensures longevity, enabling good manufacturers to offer engineering-led 100-year guarantees on their materials. Independent tests, including those for creep resistance, heat aging, ozone resistance and tensile strength, validate the effectiveness of these materials, making them a trusted choice for high-performance building isolation.
Tested to last
The complexity of designing and implementing an isolation system necessitates extensive engineering expertise. Every component, from isolation bearings to tension rods and shear keys, must be meticulously coordinated with structural supports to prevent errors. Engineers dedicate significant time to refining these details, often developing two dozen or more drawings to ensure flawless execution.
Structural engineers also account for factors such as earthquakes, wind loads, and impact forces from rail cars, making shear keys and pins indispensable in their designs. These elements are strategically placed to absorb and distribute forces, preventing excessive stress on the structure.
Testing plays an integral role in this process. Certified bearings must pass independent evaluations to verify long-term creep resistance and ensure that they maintain structural integrity over decades. Load-deflection tests confirm that bearings can withstand 1.5 times their design load without bond failure, while dynamic stiffness tests validate their vibration isolation capabilities.
Inspections matter
Once construction begins, the responsibility of maintaining isolation efficiency shifts to on-site inspections. The risk of short-circuiting increases when mechanical, plumbing and electrical systems cross the isolation plane. Proper installation of flexible connectors is necessary to ensure these systems do not inadvertently transmit vibrations. One common oversight is the installation of elevator rails that are not adequately isolated, potentially compromising the entire system.
Frequent inspections, ranging from 20 to 100 visits depending on project complexity, help identify and rectify such issues before substantial completion. Retrofitting isolation components post-construction can be expensive and, in many cases, unfeasible. This underscores the importance of meticulous planning and execution from the project’s inception.
The road ahead
The growing emphasis on sustainable urban development has reinforced the need for effective building isolation. As cities expand and more structures emerge near transportation hubs, integrating advanced isolation systems will be key to enhancing both structural longevity and occupant comfort.
Unfortunately, many buildings in urban areas were designed prior to the emergence of the tube tunnels and trainlines that have grown up around them and now cause vibration problems for building users and occupants. As well as isolating new buildings, isolating existing buildings is also an option, albeit often difficult to implement from a practical perspective.
Providing isolation to an existing building can avoid the need for costly demolitions and rebuilds. Historic buildings that are no longer commercially viable due to vibration problems can be transformed through effective structural isolation. As well as saving on cost, structural isolation of existing buildings is better for the environment. Preserving existing historic structures reduces material waste and the negative environmental impact of demolitions.
Isolating historic buildings is also better from a cultural heritage perspective. A good example is the transformation of Cambridge House in London. This historic building is being repurposed as a luxury hotel, but without isolating the existing structure the vibration problems caused by tube trains would have made the building’s transformation unviable, requiring instead a costly rebuild that would mean the loss of a historically significant building.
The success of a building isolation project hinges on early collaboration among stakeholders, precision in design, rigorous testing, and vigilant construction oversight. By adhering to these principles, developers can ensure that their projects not only meet but exceed industry standards, creating vibration-free environments that stand the test of time.